反驳炉
旋转的圆柱偏反反驳通过在一系列内部叶片上缓慢向前向前滚动的部分将部分从一端转到另一端。内部温度由Eurother 3204 PID控制器维持,并且两个位置选择器允许操作员在需要更长的停留时间时连续驱动炉子朝着一个方向驱动炉子或选择交流的交替运动。
交替循环的周期由双设定计时器控制,旋转速率由Allen-Bradley PowerFlex 525可变频率驱动器(VFD)和1 HP电动机控制,并通过900:1齿轮减速器控制。操作员通过其集成控制面板手动设置驱动器的输出频率。
淬火坦克
零件从炉子的末端通过溜槽掉入一个7,000加仑的水箱,在那里它们在水或油中冷却。淬灭剂通过由30 hp 230v 3相AC电动机驱动的固定速度泵不断循环。
输送带
由2.5 hp 230v 3相AC电动机驱动的传送带从淬火箱中取出处理的零件。
控制平台评估
鉴于其控件的范围升级(包括计算机称重,燃烧器控制和驱动器控制)AMP知道它需要定制解决方案。在收到了几个行业系统集成商的报价之后,Pinkos很明显AMP有两个选择:“我们要么付给某人6万美元,并给他们提供汽车的钥匙,要么我们考虑使用本土的解决方案。”
PinkOS联系的大多数公司都希望完全重建馈线系统电池板,包括针对新PLC和随附的HMIS进行定制编程,除非他们还支付了所需的设计软件许可证,否则AMP无法访问源代码。AMP想知道它是否可以承担工作本身,有可能降低成本,并可以选择保留其控制逻辑的全部所有权。
Pinkos解释说:“对于像我们这样的业务不到25名员工的业务,内部开发解决方案本质上比支付外部公司更具吸引力,因为它使我们可以完全控制该产品,我们可以修改,适应或修改,适应或随着我们需求的变化而扩展它。我们的过程是可以在白板上勾勒出来的东西,我们认为解决方案应该易于实施和理解。”
AMP开始研究本土解决方案所需的内容。根据Pinkos的说法,它将Opto 22确定为潜在的解决方案供应商,同时探索可追溯到1993年的馈线I/O面板。“ Opto 22 I/O模块是仍在工作的少数部分中的一些部分”。“我们有一个报价凹槽史诗般的系统并对所提供的价值和多功能性印象深刻。”
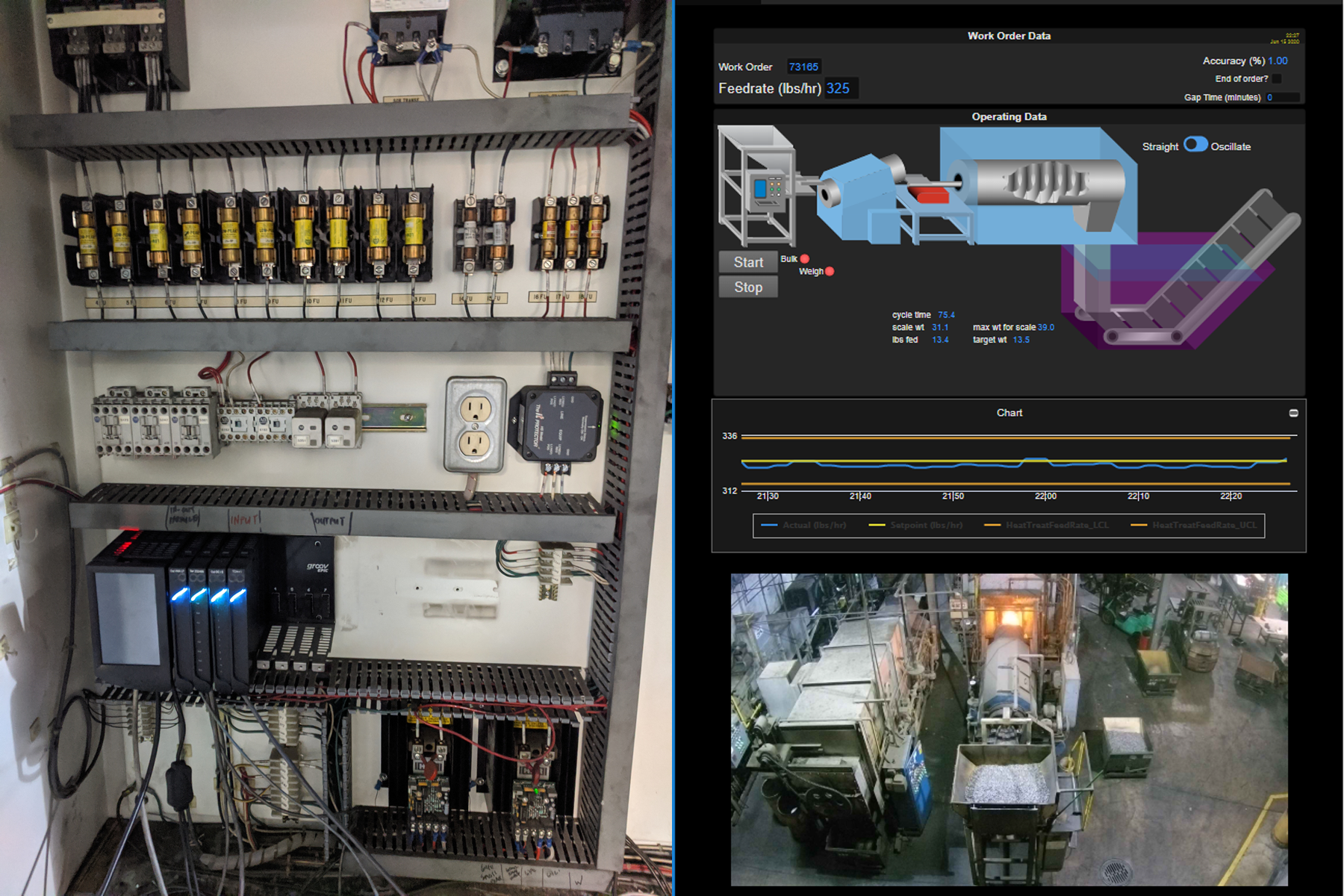
新的电动面板布局,带有groov Epic和伴随的凹槽视图HMI
由于EPIC作为其新控制系统的潜在基础,AMP开始绘制出使用Opto 22可用内容确定的目标的途径开发人员论坛, 自由培训视频, 和支持渠道。Pinkos是教育的化学工程师,开始学习Opto 22的免费PAC控制销售和支持人员的指导的编程软件。
正如Pinkos所关联的那样,经验为AMP提供了所需的方向。“我可以看到这些碎片汇聚在一起。Opto 22在教导没有编程背景的人们方面做得非常出色。当我意识到我可以使用数据记录凹槽史诗,这为我检查了另一个盒子。一旦我们找到了一种方法,可以让我们的批次跟踪数据库使用REST调用来从该数据中提取数据凹槽史诗,然后我们有一个完整的解决方案。Epic使创建本土系统成为可能。”
系统升级
AMP开始开发其第一个凹槽史诗般的系统具有分阶段计划,用于升级其七个炉子线。但是,一个月后,AMP在其中一条线上遭受了严重的PLC故障,并决定将新系统的早期版本投入使用。
建立在
凹槽史诗处理器(
grv-epic-pr1),第一个系统合并以下I/O模块,每个模块都具有通道到通道隔离,允许AMP建立一个基本的控制系统:
通过系统的串行输入之一监视馈线系统量表,两个振动阶段通过0-10 VDC输出控制。
使用一个串行输入通道将反驳炉控件集成到控制程序中,以测量炉子的旋转速度,一个用于VFD的设定点控件的模拟输出,一个离散的DC输出到VFD以控制旋转方向,并进行四个模拟输出炉体和内部气氛的温度读数。
使用额外的串行输入将输送机集成到控制程序中,以监视皮带速度。
最后,放大器凹槽EPIC连接到公司网络,完成了基本设计,为继续增强奠定了基础。
因为凹槽EPIC使用能够并行运行多个应用程序的四核ARM处理器,包括其他软件应用程序,控制逻辑只是AMP现代化程序的开始。
操作界面
包含的软件应用程序之一凹槽史诗是凹槽看法,用于创建车载,外部,移动和桌面HMI显示的嵌入式可视化服务器。同时重复先前基于PC的馈线HMI的功能凹槽查看,AMP借此机会整合了其他控制元素并创建统一的操作员界面。
炉温度,反驳速度(对应于停留时间),并将淬火储罐温度添加到现有的进料系统读取中,而手动炉计时器和旋转方向选择器组件则用HMI控制小工具代替。根据Pinkos的说法,结果是一个逻辑上安排的操作员界面“任何人都能理解”。
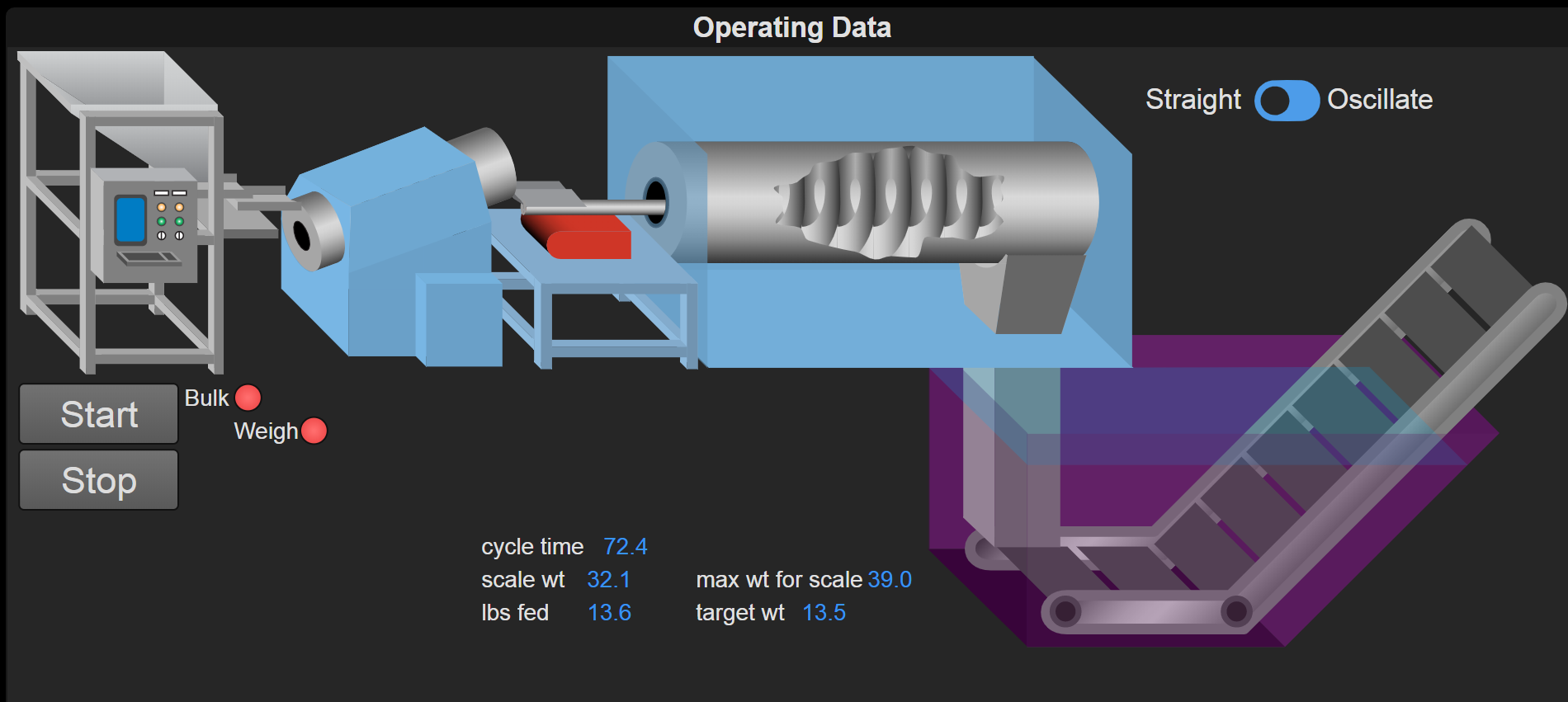
GROOV查看HMI - 操作器控制和流程读数